HISTORY
Since 1966, in the tanning history of Ponte a Egola.
Vesta Corporation has its roots in the tanning history of Ponte a Egola, where, in 1966, during the economic boom of Italian production, the individual company under the name Vesta began manufacturing leather for soles, much in demand in the emerging footwear industries.
Over the years, Vesta has expanded its product lines. Today it uses chrome-tanning and metal-free tanning to produce lightweight leather from calf and half-calf hide, as well as heavy leather from bull, rump and back hide, for haute couture and technical footwear brands.
INNOVATION and TECHNOLOGIES
The production capacity of the industrial plant of Vesta Corporation amounts to 100,000 square metres per month. In compliance with Industria 4.0 efficiency parameters, in 2019 Vesta has expanded, moving into a new facility to optimize its manufacturing cycle as well as a healthy work environment for its employees and the local communities.
Its industrial structure, which is on its way to achieving energy self-sufficiency through the installation of a photovoltaic system, covers all transformation stages, to include both the wet phase and finishing. The area dedicated to wet processing is made up of five sub-sections: raw material area, wet blue area, wet white area, riviera area with tumbling barrels and characterisation area.
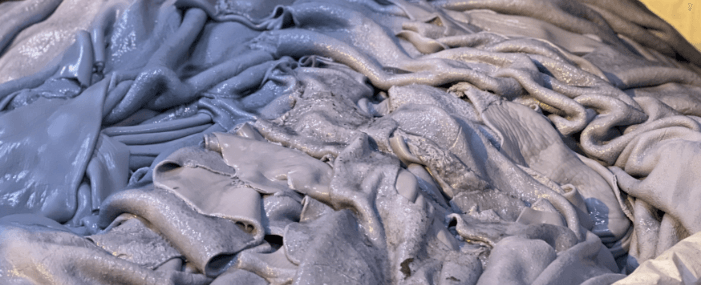
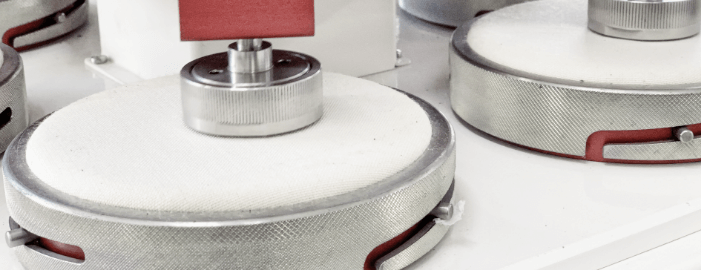
Quality Control Laboratory
Our advanced standards are measured at the beginning of the manufacturing process, during the processing phases and after the product has been completed, through physical tests carried out in-house and chemical testing conducted by an approved laboratory, validated by the issuing of an Electronic Quality (e-Quality) Certificate.
EVERY TEST CARRIED OUT IN OUR QUALITY CONTROL LABORATORY PRODUCES AN e-QUALITY (ELECTRONIC QUALITY) CERTIFICATE, AIMED AT TRACING THE PHYSICAL AND CHEMICAL CHARACTERISTICS OF THE PRODUCTION SYSTEM OVER TIME.
In order to guarantee an undisputed product quality, Vesta has set up its own quality control laboratory. This is where all physical tests are conducted to simulate the various use conditions of leather over time. This laboratory can serve for a number of tests, including: Veslic, Martindale, Bally Flexometry, Lastometer, Dynamometer, Bally Penetrometer, PVC Migration, Resistance to light/accelerated ageing and pH of the aqueous extract. These tests are carried out on a regular basis at the beginning of the production process, during the various processing phases, taking samples during the intermediate stages, and – of course – after manufacturing has been completed, with a view to ensure the final requirements of our leather products. The results of each test are included in an e-electronic quality (e-Quality) certificate that serves the purpose of tracing the physical-chemical characteristics of the production system under examination over time.
After years of testing Vesta processes, it can be concluded that our carry-over items, a consolidated stronghold in terms of technical research and manufacturing experimentation, are fully compliant with the standards in force as regards safety and health, as well as adhering to all technical quality characteristics required by customer specifications.
The quality control laboratory at Vesta Corporation SpA is equipped with the machinery required for tests according to ISO standards in force.
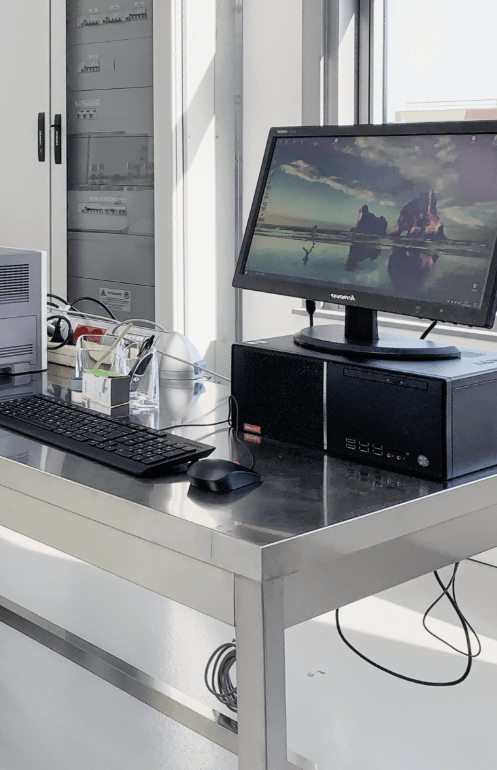
Leather – Calculation of water resistance in lightweight leather –
Part 1: Repeated linear compression (penetrometer)
UNI EN ISO 5403-1:2012
Wicking Test (Norma GORE)
Calculation of tensile strength and percentage elongation
UNI EN ISO 3376: 2012
Calculation of tear strength – Part 1 single-edge tear
UNI EN ISO 3377-1: 2012
Calculation of tear strength – Part 2 double-edge tear
UNI EN ISO 3377-2: 2006
Calculation of surface distension strength (marble method)
UNI EN ISO 3379:2015
Calculation of flex resistance
Part 1 method with dry and/or wet flexometer
UNI EN ISO 5402: 2012
Test for “TAPE TEST” finish abrasion
UNI EN ISO 11644: 2009
Test on dry and/or wet resistance to abrasion (MARTINDALE)
UNI EN 13520: 2006
Colour fading under an artificial light. Test with Xenon arc lamp
UNI EN ISO 105-B02: 2014
Effects of rubbing on colour fastness (VESLIC): dry and/or wet test
UNI EN ISO 11640: 2013 QB/T 2537: 2001
Effects of rubbing on colour fastness (VESLIC): test with synthetic Perspiration
UNI EN ISO 11640: 2013 QB/T 2537: 2001
Colour fastness to (acidic/alkaline) perspiration
UNI EN ISO 11641: 2013
Colour fastness to water stains
UNI EN ISO 15700: 2000
Colour fastness to plasticized polyvinyl-chloride (PVC)
UNI EN ISO 15701: 2001
Colour fastness to dry and/or wet Crocking
UNI EN ISO 20433: 2012
Determination of pH
UNI EN ISO 4045:2000
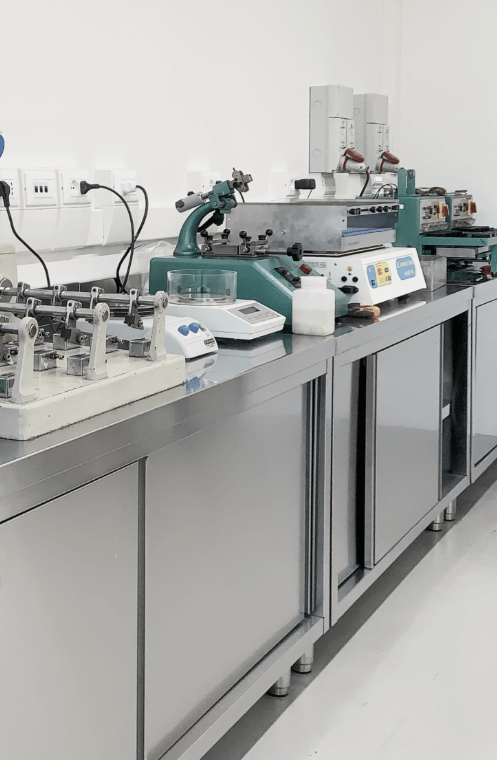
The digital printing department
Alongside creative research on processing, colouring and finishing, Vesta can enhance leather also through the digital printing of effects and patterns on surfaces.
The pattern on leather can be the result of a design concept suggested by the customers, which entails conducting a study aimed at expanding and processing it. On the other hand, Vesta is also able to engineer an existing pattern, supplied by the brand’s style department, to ensure its most effective printing on leather. Last but not least, the Research and Development lab at Vesta is constantly driving experimentation forward, by processing original suggestions, solutions, prototypes and samples, with a view to meeting current requirements or anticipating trends.
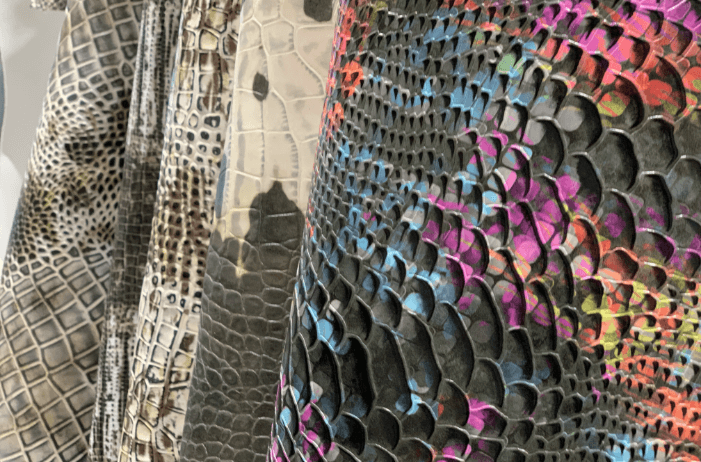
GOVERNANCE
The development and consolidation of Vesta Corporation was further boosted in 2020, with the arrival of the private equity fund Bravo Capital Partners, which acquired 70% of the company’s capital. Bravo Capital Partners has so far confirmed the guidelines established by the managing director Sauro Gabbrielli: the idea is to strive for excellence, in a product for top-of-the-range luxury brands, as well as fostering the talents of human resources and achieving sustainability in every respect.
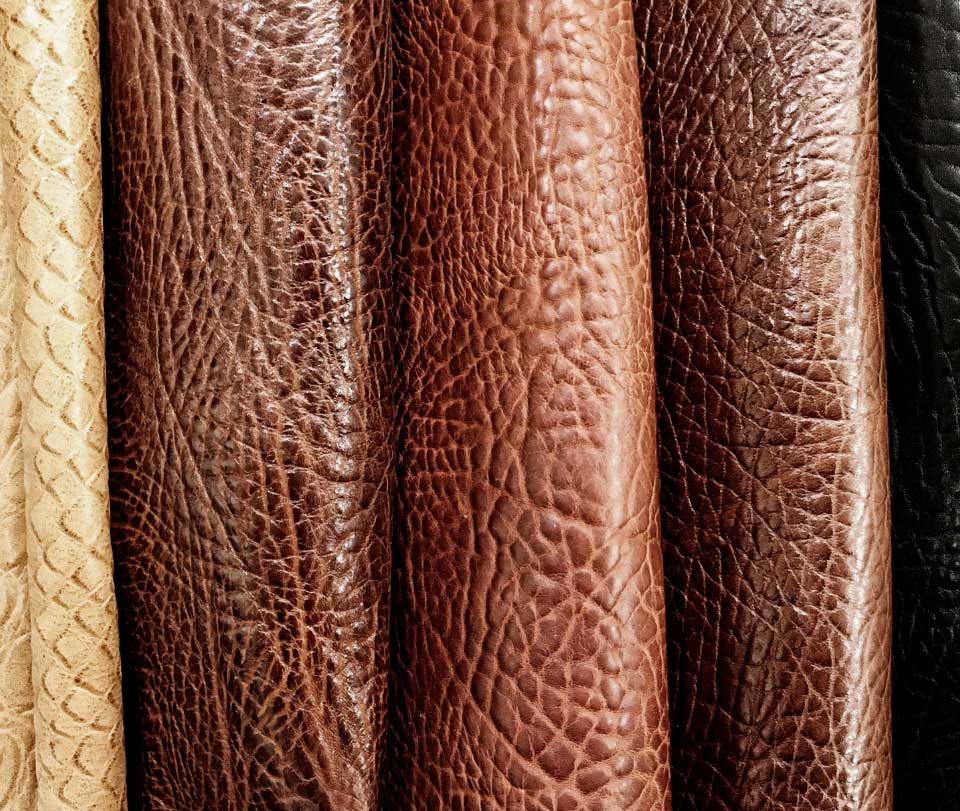